Home » Posts tagged 'moisture mapping'
Tag Archives: moisture mapping
The Different Types of Demolition
Demolition is the process of removing buildings and structures. It can be done manually or using specialized machinery. Contact Diversified Management & Construction, Inc. now!
Safety is a top priority in demolition, and choosing a contractor with experience with the type of building you want to demolish is important. Protective barriers and other safety measures are implemented, and regular monitoring helps ensure all safety standards are met.
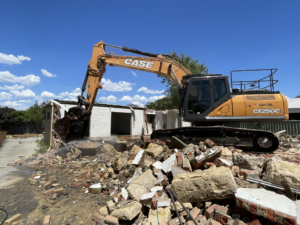
Building demolition is dismantling and destroying buildings or structures to make room for new construction. This can be done for a number of reasons, including safety issues, old age, or the desire to sell a property. It’s important to use the right equipment and techniques to ensure that the demolition is completed safely.
The first step in a successful demolition is to prepare the site. This includes installing barriers and fencing, providing protective gear to workers, and ensuring that there is clear communication on-site. Regular inspections and monitoring throughout the demolition process are also essential to maintaining high levels of safety.
Once the site has been prepared, a detailed plan of how to demolish the structure should be created. This will determine which method is best suited to the building materials and size. The plan should also include details on how to dispose of any hazardous materials and how to protect the surrounding environment.
Some buildings may need to be completely demolished while others can be partially demolished and then used for a different purpose. The choice to partially or fully demolish a structure often depends on its condition and whether it would be cost-effective to salvage certain materials.
There are many different methods that can be used for building demolition, but the most common involves using large hydraulic equipment like elevated work platforms, cranes, excavators or bulldozers. These machines can be used to manually or mechanically pull the structure down, or they can be equipped with shears that cut through metal and concrete. A wrecking ball, a heavy weight on a cable that’s swung by a crane into the side of the building, is another commonly used method for demolishing buildings.
Commercial Demolition
The process of commercial demolition differs from residential demolition in several ways. While both involve the use of heavy equipment, commercial demolition involves a much larger scale and different regulations and permits. It is also more complicated due to the presence of specialized systems such as HVAC, plumbing, and electrical components.
The first step of any demolition project is to acquire the necessary paperwork and permits. This typically includes a site inspection and will likely require the property to be marked as condemned. A qualified demolition contractor will then begin preparing the building for the actual demolition. This includes removing all contents from inside the structure and clearing the land for any safety issues or environmental concerns that need to be addressed.
Next, the demolition team will disconnect all the gas, water, and electricity lines to the building to prevent any accidents during the demolition process. This is one of the most important parts of any demolition because if these lines aren’t disconnected properly, they could become a hazard to anyone who enters the structure or is working nearby.
Once all the utility lines are disconnected, the demolition process can start. This is when the bigger machinery comes into play, and it can be a noisy, messy, and dangerous process. During this phase, the demolition team will tear down walls and floors, and it may take a while to get rid of all the debris.
The last part of the commercial demolition process is to clean up the site and recycle any materials that can be reused or sold. A quality demolition company will follow sustainable construction practices to reduce waste and ensure that the demolition site is safe for future development. They will also conduct a final inspection and documentation to make sure that the demolition project has met all safety standards and requirements.
Industrial Demolition
Industrial demolition is an in-depth, complex process that requires meticulous planning and precise execution. The specialized skills and equipment required to carry out this type of project require an experienced, licensed industrial demolition contractor. In order to minimize the impact of industrial demolition on nearby communities and businesses, it is important for industrial demolition contractors to understand and follow all relevant environmental regulations.
Before any demolition work can begin, it is essential to obtain all necessary permits from the local government. A permit application usually involves a detailed site visit, and is the first step in ensuring that all applicable environmental regulations are followed.
Once all permits are in place, the next step is to clear the building. This includes removing all furniture, equipment, and fixtures from the structure before demolition begins. This step is particularly important when reusing or recycling the demolition debris, as it helps reduce landfill waste and promotes sustainability.
It is also important to disconnect all utilities before starting demolition. This is a crucial safety measure that helps prevent dangerous accidents, such as fires or flooding. It is also important to put in place all necessary safety barriers and warning signs to keep workers and the public safe from falling debris and dust.
Post-demolition, demolition debris is typically sorted and crushed on site. This allows for the reuse of materials such as concrete, metals, and wood in future construction projects, reducing waste and saving on disposal costs. Other types of waste, such as asbestos, are removed and disposed of in accordance with all local health and safety regulations.
At the end of a project, a full project review is conducted to assess any unexpected challenges or issues. This is an opportunity to identify best practices and improve overall performance. In addition, a final report is prepared that documents the entire demolition process from planning to completion. This document serves as a valuable record and can be used for future reference and compliance audits.
Residential Demolition
Residential demolition involves the dismantling of single-family homes or multi-unit living spaces, including apartment complexes, condominiums and dormitories. While this type of demolition may not require the same level of precision as commercial demolition, it does still demand a high degree of care and safety. As such, homeowners and contractors alike should familiarize themselves with local regulations regarding permits, air quality requirements, and hazardous materials before starting any work on the property.
Before beginning the demolition process, experts will usually inspect the home for issues like lead paint, rotted wood, mold and asbestos. If any of these materials are found, remediation procedures will follow to address them before demolition begins. Next, professionals will disconnect all utilities such as water, sewage, electricity and gas to prevent damage during the teardown. They’ll also erect fences around the structure and notify nearby neighbors of their presence to ensure that everyone stays safe during the project.
Depending on the method of residential demolition chosen, it can take anywhere from a few days to several weeks for the job to be completed. It’s important to budget for permit fees, equipment rental or purchase, labor costs (if hiring professionals), and waste disposal before getting started. It’s also recommended to plan ahead for additional expenses like soil testing, site cleanup and repurposing or recycling of salvageable materials.
Because residential demolitions occur in established neighborhoods, they often affect the lives of nearby residents. To avoid disruptions to their daily routines, residents should communicate with their contractor before the project starts to discuss schedules and expectations. This can include letting neighbors know that the demolition will create dust, noise and traffic. It’s also a good idea to notify mortgage lenders so they can update their records before the demolition begins.
Brownfield Demolition
A brownfield is real property, the expansion, redevelopment or reuse of which may be complicated by the presence or potential presence of a hazardous substance, pollutant or contaminant. Often, the contamination is the result of past industrial activity such as manufacturing, railroad depots, dry cleaners and gas stations. In urban, suburban and rural communities, the cleanup of these properties and their reuse as viable commercial, retail, housing or recreational areas can create jobs, foster economic development and revitalize neighborhoods that might otherwise be abandoned or left to deteriorate.
The EPA reports that there are thousands of these sites across the country – and the list continues to grow. The costs of identifying and remediating these sites can be high, but the long-term benefits of their redevelopment are even greater. Using old, abandoned or underused land for new development can create jobs, boost tax revenue and improve community health and safety.
Brownfield cleanup can also reduce risk and prevent future environmental harm. For example, if a site is contaminated with dangerous chemicals, the groundwater could be threatened. In addition, contaminants can be stored in soil or buildings, and if they leach into the environment, they can pose a threat to public health and the economy.
Fortunately, the EPA has a number of programs that can help address brownfield issues. One such program is the Brownfield Remediation Assistance Grant, which provides financial support to help communities explore and address the challenges of developing a brownfield. Another is the Brownfields Revolving Loan Fund, which helps finance assessment and cleanup activities.